Ergonomie first: Wie die neuen Akku-Bohrschrauber zu echten MAFELL Produkten wurden. Eine Entwicklungsgeschichte.
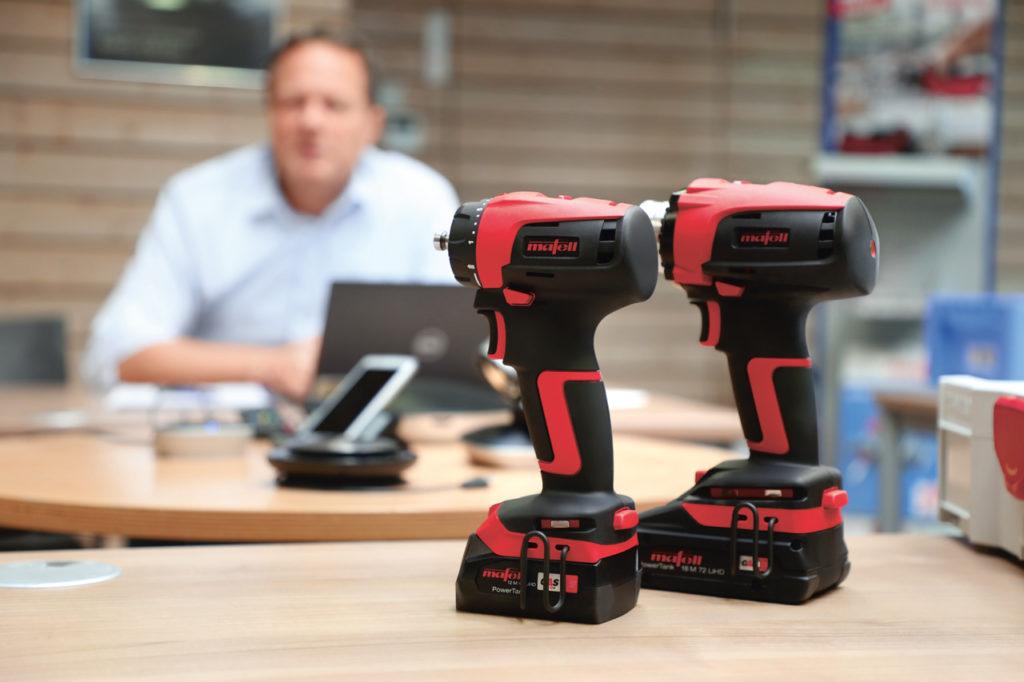
Foto: MAFELL AG
„Niemand von unseren Kunden braucht eine MAFELL Maschine, die genauso ist wie alle anderen.“ Davon ist Jörg Betsch, verantwortlicher Produktmanager, überzeugt. Er versteht es, uns den immensen Aufwand, der in jedem neuen Produkt steckt, anschaulich zu beschreiben. Das Ziel sei immer das gleiche: auf die tagtäglichen Herausforderungen der Kunden fühlbar besser einzugehen als andere. Dieser Anspruch ist extrem hoch, doch die Kunden wissen ihn zu schätzen. „Eine Maschine im Mittelfeld rauszubringen, macht für uns keinen Sinn“, sagt Betsch.
Teilweise dauert es Jahre, bis eine neue MAFELL Maschine so gut und ausgereift ist, dass sie in die Serienproduktion gehen darf. Bis dahin durchläuft sie eine Reihe von Entwicklungsstufen. Doch zuallererst schauen sich die Produktmanager den Markt und die Mitbewerber an, testen deren Maschinen auf Herz und Nieren: Was können sie gut, was nicht?
Im Lastenheft definiert das Produktmanagement dann unter anderem sehr detailliert, was das neue Gerät können muss. Ein aktuelles Beispiel sind die neuen Akku-Bohrschrauber. „Da steht dann drin, wie viele Schrauben die Geräte ohne Murren eindrehen müssen und dass sie einen Sturz aus vorgegebener Höhe überstehen müssen“, berichtet Konstrukteur Samuel Gühring.
Samuel Gühring ist einer derjenigen, die alles, was im abgesegneten Lastenheft steht, bestmöglich umsetzen müssen. Natürlich sind im Lastenheft noch zahllose weitere Anforderungen aus Marktsicht definiert: von der vorgesehenen Anwendergruppe über technische Features, Abmessungen und Gewicht bis hin zu Ausstattungsvarianten und geplantem Zubehör. Auch die Anwendungsnutzen und die Vorteile gegenüber Produkten der Mitbewerber sind klar vorgegeben. „Da stehen oft sehr ambitionierte Dinge drin, die auf den ersten Blick oft gar nicht umsetzbar scheinen“, verrät Gühring.
„Das ist wie beim Schuh: Der kann super aussehen und verarbeitet sein – wenn er drückt, zieht man ihn trotzdem nicht an.“ – Jörg Betsch über Ergonomie bei Elektrowerkzeugen
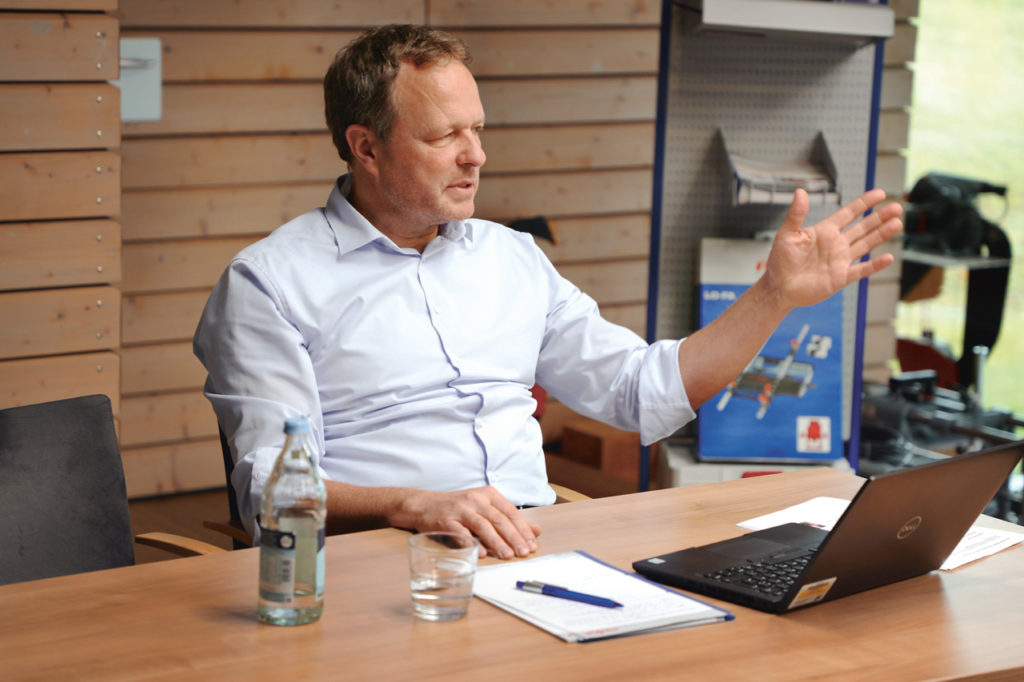
Foto: MAFELL AG
Am Anfang einer Neuentwicklung steht bei MAFELL immer eine Idee oder ein bekanntes Anwenderproblem. Jörg Betsch ist regelmäßig unterwegs bei Kunden und hält die Ohren offen. Wenn Handwerker ihm erzählen, dass ihnen abends das Handgelenk vom Halten des Schraubers wehtut oder Schalter sich schlecht mit einer Hand erreichen lassen, weiß er, wo er im Lastenheft ansetzen muss.
MAFELL ist bekannt für eine hohe Fertigungstiefe. Nur wenige Komponenten eines Produkts werden nicht direkt in Oberndorf entwickelt und hergestellt.
Das habe einen großen Einfluss auf die Qualität der Produkte, weil man nicht vom Qualitätslevel der Lieferanten abhängig ist, betont Jörg Betsch. „Trotzdem gibt es Dinge, die wir – genau wie andere – nicht selbst machen, weil es dafür exzellente Spezialisten gibt. Aber sie müssen natürlich bestmöglich zu unseren hohen Anforderungen passen.“
Die neuen Akku-Bohrschrauber sind in diesem Punkt ein Sonderfall. „Ein Akkuschrauber ist kein klassisches MAFELL Produkt, aber unsere Kunden fragen ihn bei uns nach, weil sie unseren Qualitätsanspruch kennen“, berichtet Jörg Betsch. Deshalb hat MAFELL sich entschlossen, den Antriebsstrang der Schrauber eines Partners zu übernehmen, der hier eine hohe technische Expertise mitbringt. Dennoch sind die Neuen letztlich erst in Oberndorf zu MAFELL Produkten geworden.
„In unseren Lastenheften stehen oft sehr ambitionierte Dinge, die auf den ersten Blick gar nicht umsetzbar scheinen.“ – Samuel Gühring, Konstrukteur
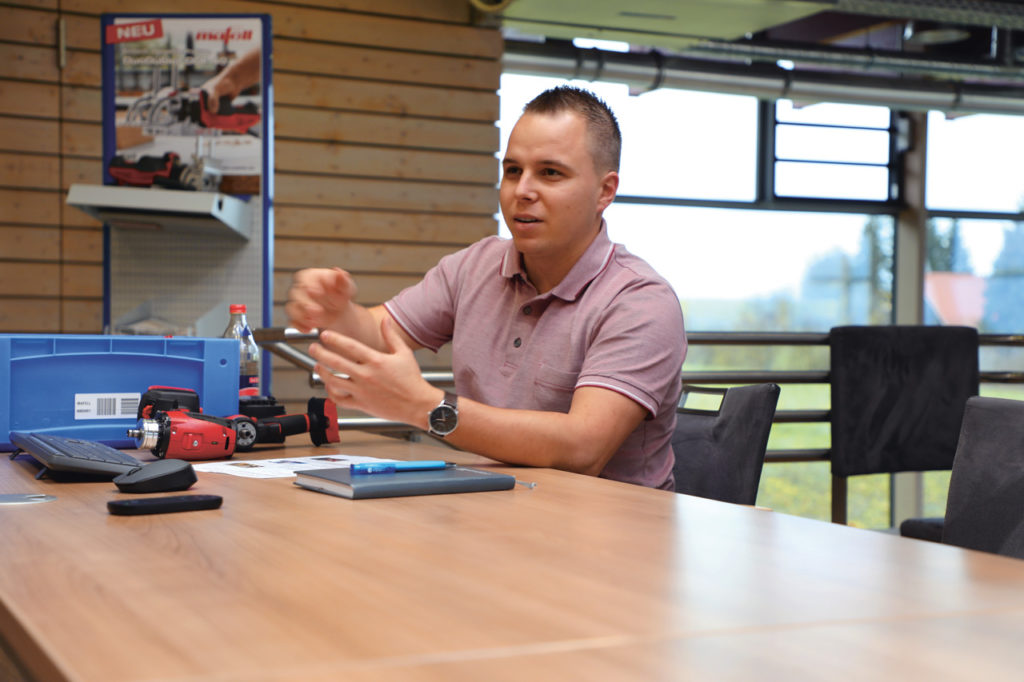
Foto: MAFELL AG
Akkuschrauber sind auf den ersten Blick relativ simple Werkzeuge und geben funktional nicht viel Spielraum für neue Entwicklungsansätze. Beste Kontrolle, Balance und Sicherheit sind jedoch im Alltag entscheidende Faktoren. „Für unsere Handwerker ist Ergonomie sehr wichtig, weil sie die Werkzeuge oft stundenlang in der Hand haben“, weiß Betsch. Mal über Kopf oder an beengten Stellen, mal waagerecht, mal senkrecht, mal mit nur einer Hand. Wenn dann etwas drückt, rutscht, kippt oder wenn man einen Krampf in der Hand bekommt, dann passe das nicht zum MAFELL Anspruch. „Das ist wie beim Auto: Wenn es super fährt, man aber wegen der Sitze nach ein paar Stunden Rückenschmerzen hat, dann hat man keine Freude an dem Wagen – erst recht nicht, wenn er ein Arbeitsmittel ist, mit dem man sein Geld verdienen muss.“
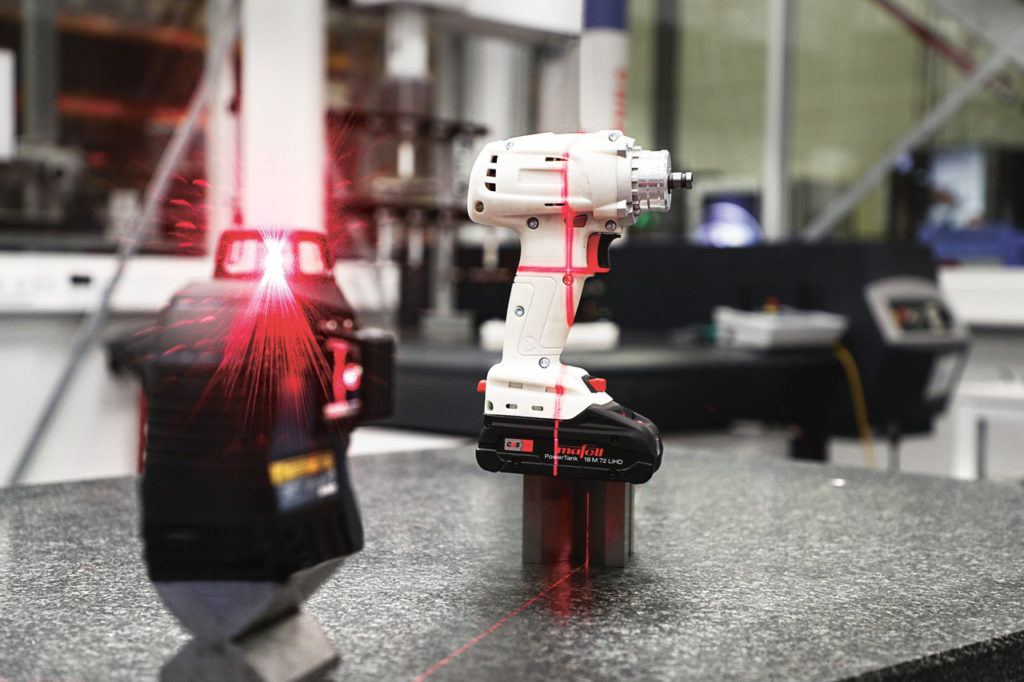
Foto: MAFELL AG
Beim Akkuschrauber spürt man sofort, ob er gut in der Hand liegt oder ob irgendwas nicht passt: Ist er gut ausbalanciert? Fühlt er sich gut an? Ist er leicht zu handhaben? Kommt man bequem an die Schalter? Ein Beispiel: Damit das Werkzeug die Hand vorne nicht nach unten zieht, war Samuel Gühring lange auf der Suche nach dem optimalen Schwerpunkt der Schrauber – bis diese zuletzt in der Balance standen, ohne dass dafür eine besondere Kraft im Handgelenk nötig war. Das hat einige Zeit gedauert. „Aber beste Ergonomie ist uns eben wichtiger als eine kurze Time-to-Market“, sagt Gühring.
Genau deshalb hat er auch an allen Hauptgreifflächen spezielle Weichkomponenten eingesetzt. Der Grund: Bei schwitzigen Händen wird der Griff gerne nass und glitschig, und das kann fatal für die Maschine und den Anwender sein. Dank der perfekten Haptik der MAFELL Schrauber hat der Anwender jetzt immer ein griffiges Gefühl und die Maschine optimal unter Kontrolle. Denn die Weichkomponente ist überall da, wo man in der Praxis hinfasst.
Beim Akku setzt MAFELL auf die Technik des Cordless Alliance System (CAS). Das hat zwei entscheidende Vorteile. Erstens gehörten die dort verbauten Akkuzellen zu den leistungsfähigsten auf dem Markt, sagt Betsch. Und zweitens findet der Handwerker bei den vielen Herstellern der Akku-Allianz fast immer eine benötigte Spezialmaschine, die dann das gleiche Akkusystem verwendet wie zum Beispiel seine Akkuschrauber.
Unterstützung holen sich die MAFELL Ingenieure bei Neuentwicklungen von externen Produktdesignern. Die kümmern sich nicht um das schicke Aussehen, wie viele glauben, sondern auch um spezielle Lösungen für optimale Ergonomie, Balance und vieles mehr. Auch hier folgt die Form immer der Funktion. Gleichzeitig muss das äußere Design aber gerade in dieser Qualitätsliga widerspiegeln, was die Maschine ausmacht, betont Betsch.
„Der Traum jedes Produktmanagers ist, mal was völlig Neues zu machen. Und manchmal klappt das sogar.“ – Jörg Betsch über den Traum eines Produktmanagers
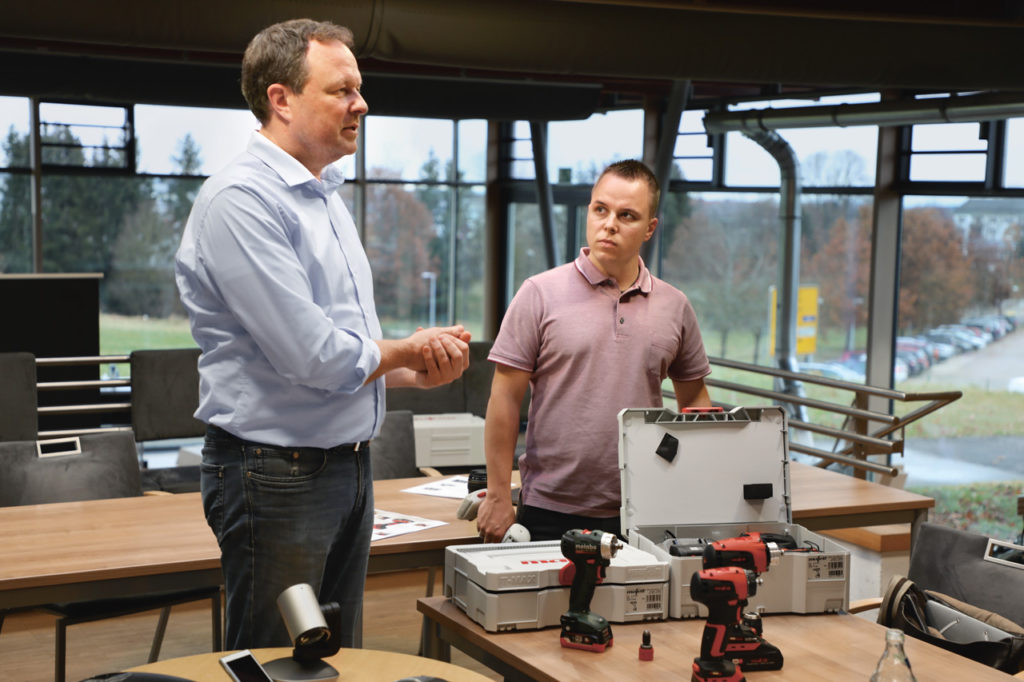
Foto: MAFELL AG
Auch in den Design-Details zeigt sich, wie intensiv Konstrukteur und Produktdesigner die neuen Akkuschrauber mit Blick auf den Anwender durchdacht und optimiert haben. Ein perfektes Beispiel ist der neu gestaltete Bithalter, der vollständig in den Griff integriert ist. Die Frage war nur: Sollte er formschlüssig sein oder magnetisch? Nach vielen Tests erwies sich die Kombiform als ideale Lösung: Der Bit ist dank Magnet bequem seitlich anzulegen, findet seine Position praktisch von allein und ist durch den Formschluss trotzdem vor Abstreifen geschützt. So hilft exzellentes Design dem Handwerker, optimale Arbeitsergebnisse zu erzielen. Ein weiteres Beispiel für clevere Details sind die zwei Libellen hinten und oben an der Maschine.
Sie helfen, speziell in schwierigen Schraubpositionen oder bei langen Schrauben, diese kontrolliert im 90-Grad-Winkel einzudrehen – in horizontaler genauso wie in vertikaler Position.
Fotos: MAFELL AG
Um am Ende die optimale Form, verbunden mit optimaler Funktion, zu erhalten, standen auf dem 3D-Drucker unzählige Muster der neuen Akkuschrauber. Hier hat Samuel Gühring nach Möglichkeit immer alle Funktionen integriert: „Bilder und Zeichnungen sind schön und gut, aber die meisten Leute können sich ein Werkzeug besser vorstellen, wenn es vor ihnen steht und sie es spüren können.“ Die „Leute“, damit ist das Entwicklungsteam gemeint, das regelmäßig ein Feedback zum aktuellen Entwicklungsstand gibt. Dazu gehören auch die MAFELL Anwendungstechniker, die neue Produkte intensiv testen. Genau wie die Kunden sind sie selbst Tischler/Schreiner und Zimmerer und decken Optimierungspotenziale gnadenlos auf. So ergibt sich immer wieder Potenzial für Feintuning, bevor die Produkte in die Umsetzung gehen.
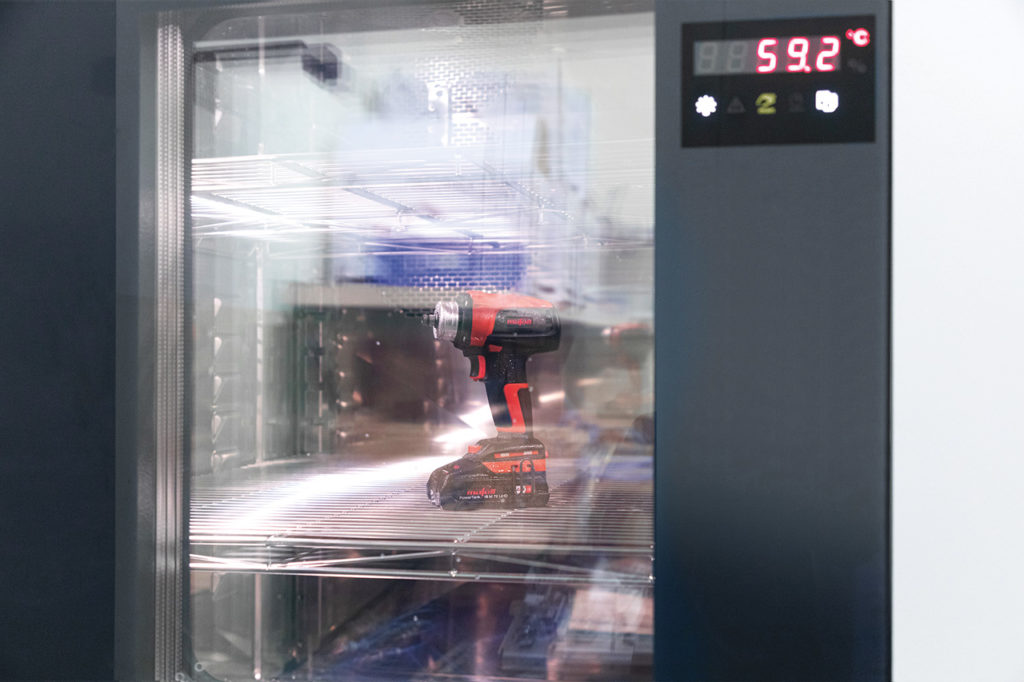
Foto: MAFELL AG
Jedes neue MAFELL Produkt muss zuvor noch einen harten Dauertest bestehen. Unzählige Betriebsstunden bringen Mitarbeiter auf die Maschine. Nur zu einem kleinen Teil geht so etwas automatisiert, denn reale Lastfälle lassen sich kaum simulieren. So auch bei den neuen Akkuschraubern. Wenn die Tester Feierabend hatten, legten sie die Maschinen bei tropischen 60 Grad und 95 Prozent Luftfeuchte in die Klimakammer, am nächsten Abend bei minus 20 Grad in die Gefriertruhe. Und das im Wechsel immer wieder. Erst wenn neue Maschinen diese Tests wegstecken, ist alles gut. „Wir testen deutlich härter, damit uns Dinge auffallen, die andere Hersteller mit anderen Zielgruppen gar nicht entdecken“, sagt Jörg Betsch. „Durch den großen Entwicklungsaufwand sind unsere Maschinen immer etwas teurer als andere. Aber wenn ein Kunde durch die hohe Zuverlässigkeit unserer Produkte auch nur einen einzigen Ausfall vermeiden kann, hat sich die Investition für ihn oft schon bezahlt gemacht.“
